Ultimate Guide to Selecting the Best Industrial CNC Plasma Table for Your Business
In today's competitive manufacturing landscape, the right tools can significantly impact the efficiency and quality of production processes. Among these essential tools is the industrial CNC plasma table, a versatile machine designed for high-precision cutting applications. As industries increasingly rely on automation to streamline operations, selecting the best industrial CNC plasma table for your business becomes a critical decision. This guide aims to navigate the complex features, types, and specifications available in the market, providing valuable insights into what to look for when investing in this technology. Whether you're in metal fabrication, automotive, or custom manufacturing, understanding the capabilities and benefits of an industrial CNC plasma table will empower you to make informed choices that enhance productivity and drive growth in your operations.
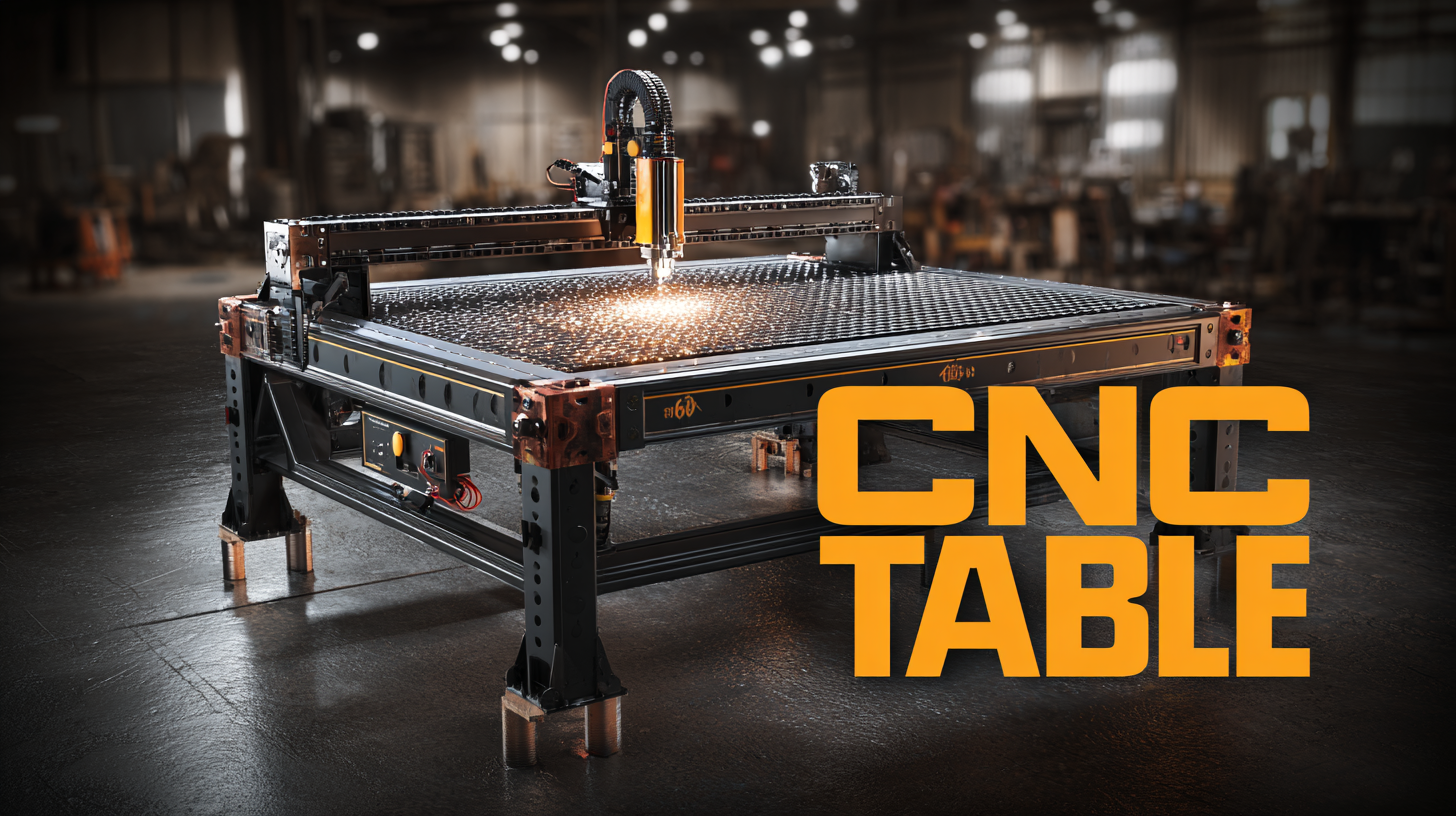
Understanding the Basics of CNC Plasma Cutting Technology for Industrial Use
CNC plasma cutting technology has revolutionized the manufacturing industry, providing precision and efficiency in metal fabrication. According to a report by MarketsandMarkets, the global CNC plasma cutting machine market is projected to reach $4.58 billion by 2025, driven by the surge in demand for automated solutions in various industrial applications. This growth is largely attributed to the technology's ability to cut through a wide range of materials, including steel, aluminum, and copper, with remarkable speed and accuracy.
Understanding the essentials of CNC plasma cutting is crucial for businesses looking to invest in this technology. At its core, CNC plasma cutting involves the use of a high-velocity jet of ionized gas (plasma) to melt and blow away material from the workpiece. This process allows for intricate cuts and designs that traditional methods, such as oxy-fuel cutting, may struggle to achieve. Industry statistics indicate that companies employing CNC plasma systems can enhance production speed by up to 50% compared to manual cutting processes, making it an ideal choice for high-volume production environments. With its cost-effectiveness and reduced material waste, CNC plasma cutting stands out as a competitive solution for modern manufacturing needs.
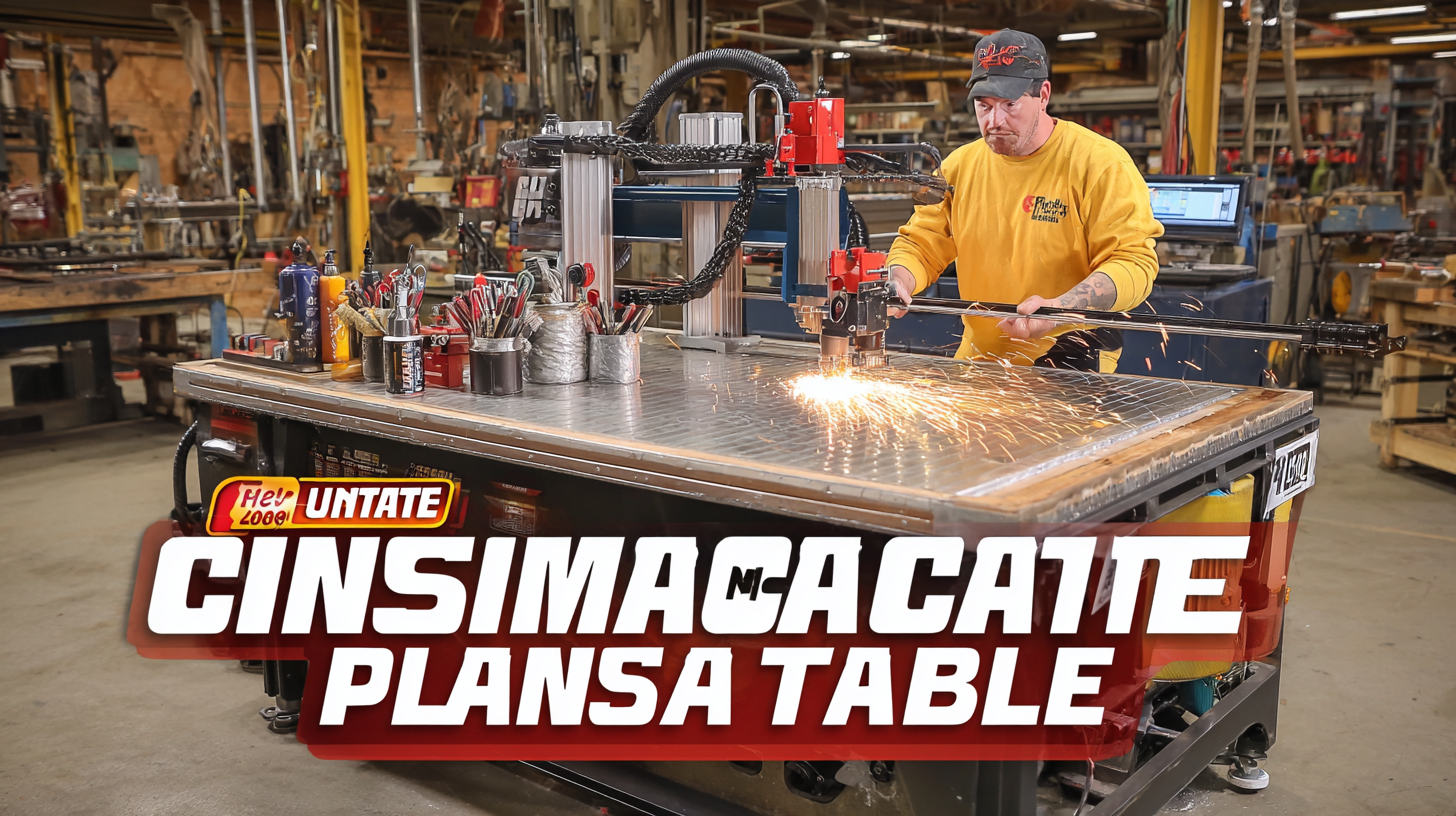
Key Features to Look for in an Industrial CNC Plasma Table
When selecting the best industrial CNC plasma table for your business, it's essential to prioritize key features that will drive efficiency and productivity. One major consideration is the cutting speed and precision. CNC plasma cutting machines are growing in demand, with the market projected to reach USD 1.1 billion by 2034, reflecting a significant compound annual growth rate (CAGR) of over 10% from 2024. This growth indicates the increasing reliance on advanced plasma technology in various manufacturing sectors, which enhances both speed and accuracy in material processing.
Another critical feature to look for is the cutting thickness capability of the plasma table. Industrial applications often demand a versatile machine capable of handling a range of material thicknesses, from thin sheets to more substantial components. Reports project that the global plasma technology market size will reach around USD 4.83 billion by 2030, demonstrating the crucial role of innovative machines in efficient production processes. Furthermore, incorporating automation features, such as integrated software solutions for design and operation, can significantly streamline your workflow while minimizing manual errors, ultimately leading to an increase in profitability as businesses evolve in response to market demands.
Evaluating Your Business Needs: Customization vs. Standard Models
When selecting an industrial CNC plasma table, understanding your business needs is crucial. One key consideration is whether to opt for customized models or stick with standard options. According to a report by IBISWorld, the demand for CNC machining services has increased by an impressive 5.2% annually over the last five years, highlighting the growing importance of tailored solutions in increasing operational efficiency. Customization allows businesses to tailor specifications, such as cutting size and thickness capabilities, which can lead to more precise and faster outputs, significantly impacting production time and costs.
Standard models, on the other hand, often come with lower initial investments and shorter lead times, making them attractive for businesses looking for quick solutions without the need for extensive customization. However, a study from Grand View Research reveals that companies investing in customized machinery tend to see a 25% improvement in productivity compared to those using standard models. Balancing your immediate budget against long-term productivity gains is key to making the right decision for your specific applications, particularly as the industry continues to evolve with advancements in technology and increased competitive pressure.
Comparison of CNC Plasma Table Features
Cost Analysis: Budgeting for Purchase and Maintenance of CNC Plasma Tables
When budgeting for the purchase and maintenance of CNC plasma tables, it’s essential to consider both the initial costs and recurring expenses. According to a recent industry report from IBISWorld, the average cost of industrial CNC plasma tables ranges from $25,000 to $150,000, depending on size, features, and brand. It's crucial to not only factor in the purchase price but also consider the costs of essential accessories, software, and installation, which can add an additional 20-30% to your initial investment.
Maintenance is another key component of your budget. A well-documented study by the Fabricators & Manufacturers Association highlights that annual maintenance can account for approximately 5% of the asset's value. Therefore, factoring in regular servicing, replacement parts, and unexpected repairs is vital. Businesses should allocate funds to ensure their CNC plasma tables operate efficiently, minimizing downtime.
**Tip:** When selecting a CNC plasma table, consider models that offer warranty and service packages. This can significantly reduce long-term maintenance costs. Also, investing in training for your team can enhance operational efficiency and extend equipment lifespan, ultimately contributing to a better return on investment.
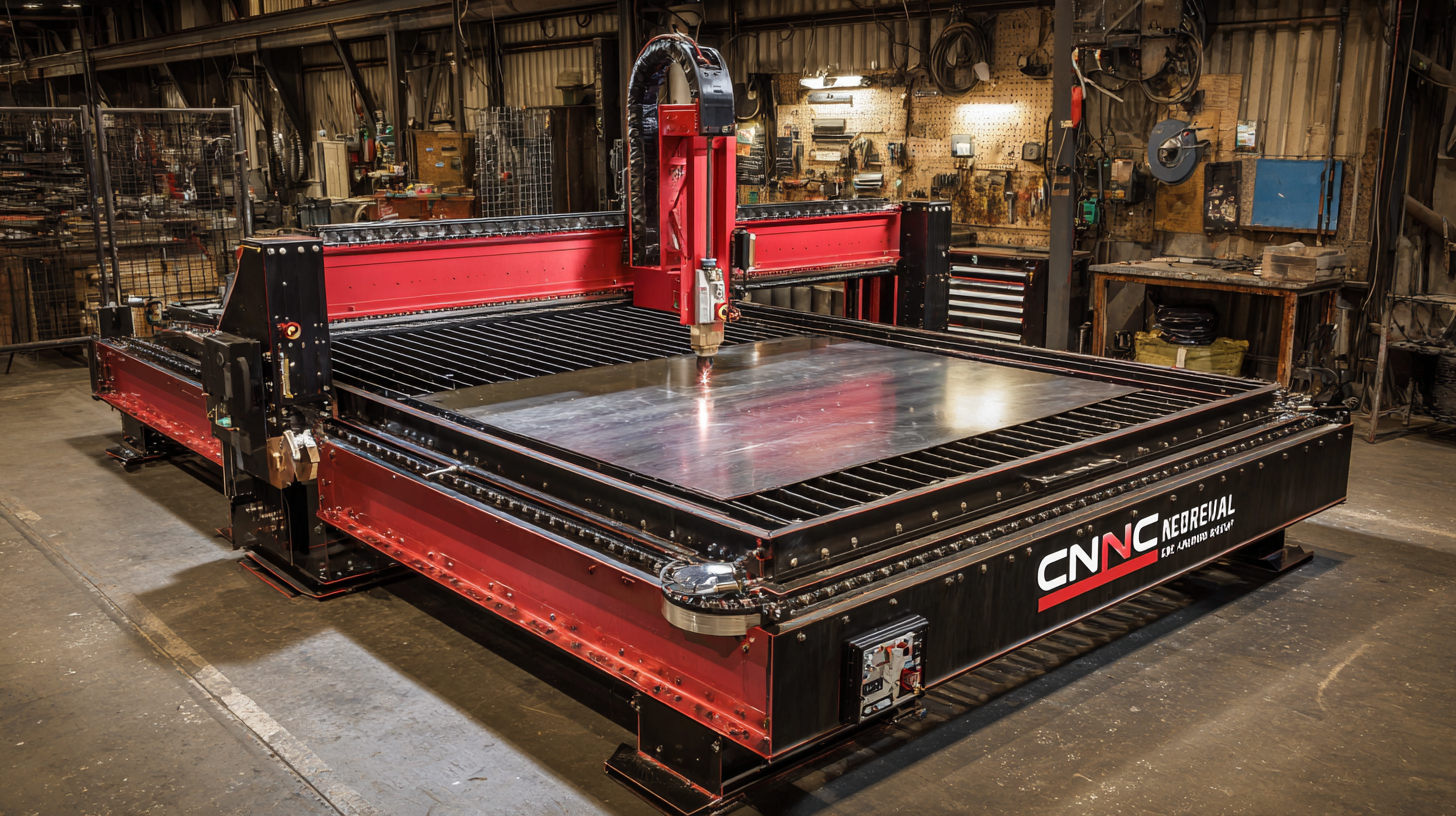
Supporting Local Manufacturing: The Benefits of Choosing Chinese CNC Solutions
When considering the future of manufacturing, choosing local solutions can make a significant difference for businesses looking to integrate CNC plasma tables into their operations. Supporting Chinese CNC manufacturers not only strengthens the local economy but also fosters innovation and quality in industrial equipment. With rigorous standards and a keen understanding of market demands, these manufacturers provide cutting-edge technology that meets the specific needs of various industries, from metalworking to automotive.
Moreover, selecting Chinese CNC solutions offers several advantages, including cost-effectiveness and responsive customer support. Chinese manufacturers are becoming increasingly competitive on the global stage, often providing high-quality products at lower prices compared to their international counterparts. This affordability, combined with shorter lead times and localized service, enables businesses to enhance their production capabilities without breaking the bank. Additionally, by cultivating relationships with local suppliers, companies can access ongoing support and maintenance, ensuring that their CNC machines operate at peak performance.
Ultimate Guide to Selecting the Best Industrial CNC Plasma Table for Your Business - Supporting Local Manufacturing: The Benefits of Choosing Chinese CNC Solutions
Feature | Description | Benefits | Price Range (USD) |
---|---|---|---|
Cutting Width | Standard widths between 4 to 10 feet | Ability to accommodate large projects | $5,000 - $15,000 |
Cutting Speed | Ranges from 2 to 5 inches per minute | Increased production efficiency | $4,000 - $12,000 |
Software Compatibility | Supports various CAD/CAM software | Flexibility in design and manufacturing | $3,000 - $10,000 |
Construction Material | Steel frame for durability | Longer lifespan and lower maintenance costs | $6,000 - $18,000 |
Customer Support | 24/7 customer service and support | Minimized downtime and operational stability | Included in purchase |